Koncepcja Lean Manufacturing została wprowadzona w rosyjskich przedsiębiorstwach nie tak dawno temu, w porównaniu z zagranicą, gdzie filozofia Kaizen zaczęła być stosowana w latach 50. XX wieku. Dziesięć lat temu tylko jedna trzecia rosyjskich przedsiębiorstw przemysłowych była zainteresowana optymalizacją produkcji. Obecnie z budowy wydajnych systemów produkcyjnych, poza dyskretną produkcją przemysłową i doradztwem, korzystają nie tylko duże, ale i średnie firmy z wielu sektorów gospodarki.
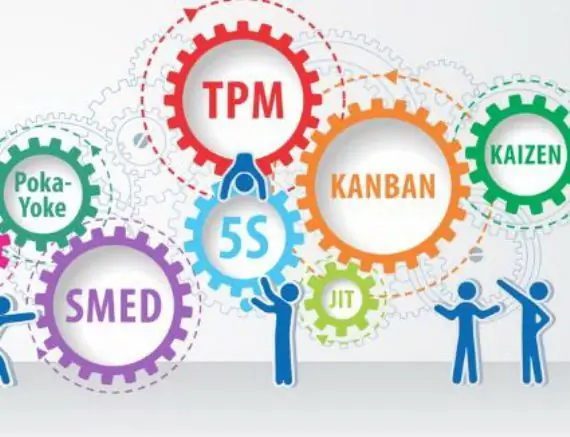
Protoplastami szczupłego systemu produkcyjnego są giganci motoryzacyjni Ford i Toyota. Wśród zagranicznych firm, które z powodzeniem stosują zasady Lean production, takie jak Nike, Textron, Parker, Intel, za początek aktywnego wykorzystania technologii Lean w naszym kraju uważa się rok 2006, kiedy odbyło się Pierwsze Rosyjskie Forum Lean. Pionierami w tworzeniu krajowych systemów odchudzonej produkcji są nasi znani producenci samochodów - GAZ i KAMAZ. Rusal, Rosatom, Eurochem, TVEL, Sbierbank i wiele innych przodują wśród firm stosujących systemy i metody optymalizacji Lean.
Wdrożenie logistyki lean manufacturing w rosyjskich przedsiębiorstwach ma wsparcie państwa i jest regulowane przez kluczowe standardy: GOST o numerach R 57522-2017, R 57523-2017, R 57524-2017, a także zalecenia branżowe zatwierdzone rozporządzeniem Ministerstwa Przemysłu i handel.
Termin „odchudzona produkcja” lub LIN jest semantycznym tłumaczeniem angielskich definicji „odchudzonej produkcji”, „odchudzonej produkcji” i transkrypcji ich skrótu LEAN.
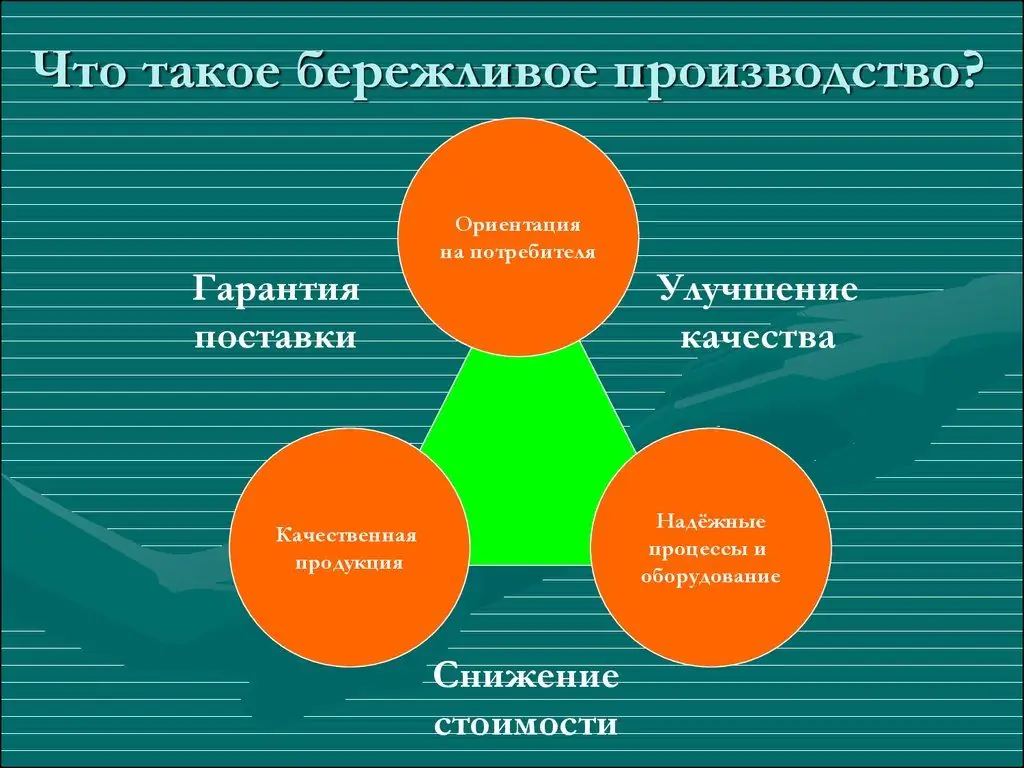
Lean production rozumiany jest jako system zarządzania przedsiębiorstwem, który pozwala na poprawę jakości pracy przy jednoczesnej redukcji kosztów poprzez redukcję strat.
W angielsko-rosyjskim tłumaczeniu słowa chudy jest „chudy, chudy, smukły”. Aby stać się takim, musisz stracić nadmiar tłuszczu. W odniesieniu do sfery produkcyjnej oznacza to konieczność pozbycia się strat, a tym samym obniżenia kosztów. Dlatego szczupła produkcja jest czasami nazywana szczupłą.
Trzy koncepcje produkcji LIN
Istotę produkcji Lean opisał G. Ford, który powiedział:.
W systemie Lean Manufacturing podstawowe znaczenie mają dwa aspekty:
- Niezbędne jest zaangażowanie każdego pracownika firmy w procedury optymalizacyjne.
- Przedsiębiorstwo powinno być maksymalnie skoncentrowane na interesie konsumenta.
Koncepcyjnie globalny system optymalizacji produkcji opiera się na trzech zasadach.
- Filozofia Kaizen. Są to mechanizmy zarządzania oparte na idei ciągłego doskonalenia jakości oraz jej operacyjnej i etapowej realizacji. Strategia Kaizen opiera się na stwierdzeniu, że nie ma granic w doskonaleniu procesów produkcyjnych i każda firma, niezależnie od swojej konkurencyjności, musi iść do przodu.
- Koncepcja Six Sigma opiera się na tym, że można zarządzać produkcją na zasadzie mierzalności dowolnych danych. Ponieważ procesy produkcyjne są mierzone, można je monitorować, a tym samym ulepszać, analizując np. kluczowe wskaźniki wydajności KPI. Koncepcja ma na celu uczynienie wszystkich procesów produkcyjnych przewidywalnymi i przewidywalnymi, ulepszanie istniejących oraz tworzenie nowych algorytmów optymalizacji.
- Poprawa wydajności produkcji, poprawa jakości wytwarzanego produktu, przy jednoczesnej redukcji kosztów - to zadania systemu Lean Manufacturing.
Razem te trzy koncepcje pokazują, jak stopniowo i stale poprawiać jakość procesów produkcyjnych i produktu końcowego bez ponoszenia zbędnych kosztów.
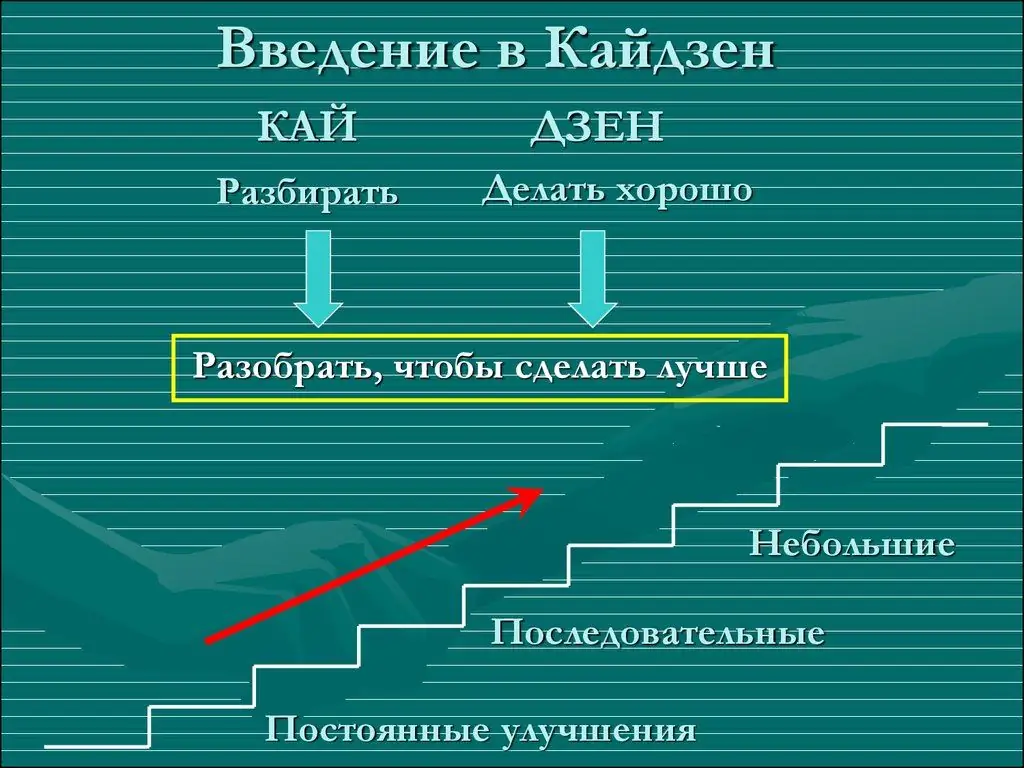
Tym samym radykalizm w zarządzaniu produkcją został zastąpiony przez zintegrowaną filozofię, która wykorzystuje idealistyczne zasady liberalnych metod zarządzania przedsiębiorstwem oraz wdraża skuteczne metodyki i narzędzia doskonalenia pracy.
Narzędzia szczupłe
Technologie Lean są wykorzystywane na wszystkich etapach działalności przedsiębiorstwa - od wstępnego projektowania procesów produkcyjnych po sprzedaż produktów konsumentowi.
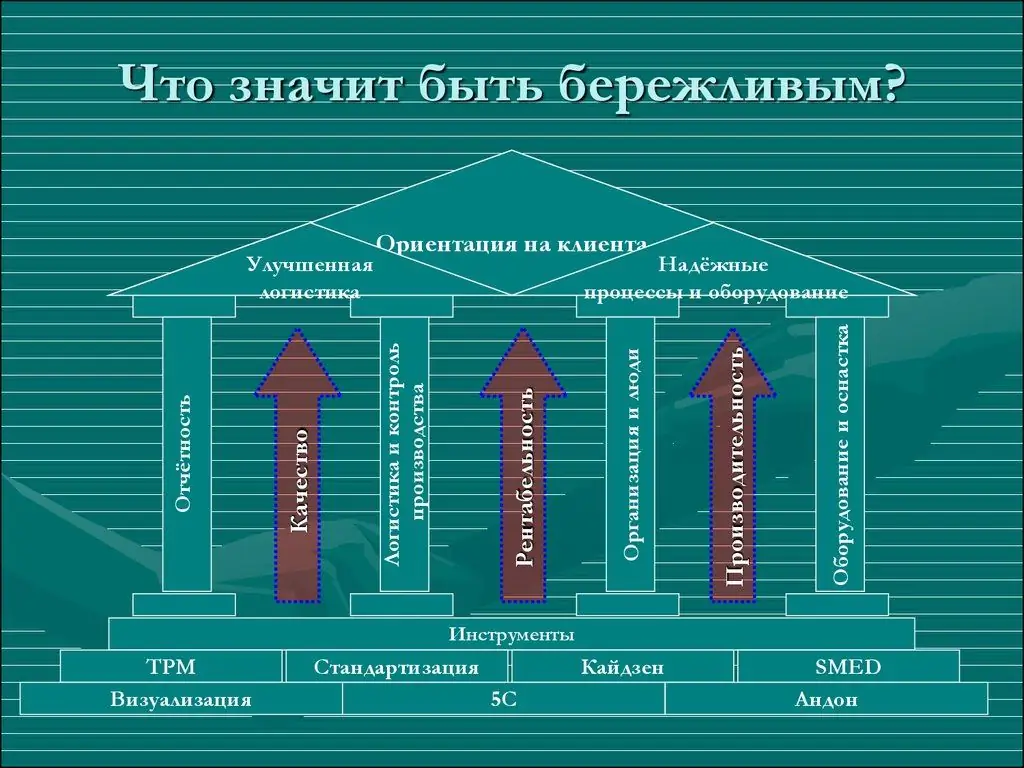
Ciągły proces optymalizacji realizowany jest za pomocą narzędzi Lean:
- Kompleksowa konserwacja produkcyjna sprzętu - TPM (Total Productive Maintenance).
- Szybka wymiana i przezbrojenie sprzętu „w ciągu jednej minuty” i „jednym dotknięciem” - SMED (jednominutowa wymiana matryc) i OTED (jednoprzyciskowa wymiana matryc).
- Organizacja ciągłego przepływu materiałów - CANBAN.
- Produkcja ciągnąca - produkcja ciągnąca.
- Mapowanie strumienia wartości - VSM (mapowanie strumienia wartości).
- System gospodarki materiałowej „just in time” - JIT (Just-In-Time).
- System zarządzania wizualnego i informacji zwrotnej Andon.
- Standaryzacja Wykonywania Pracy - Standardowe Procesy Operacyjne SOP.
- Technologia tworzenia efektywnego miejsca pracy - 5S lub 5S -CANDO.
- Kompletny system zarządzania jakością - TQM (Total Quality Management).
Narzędzia Lean działają w taki sposób, że poprawa jakości pracy jest maksymalizowana i oceniana na wszystkich etapach i poziomach produkcji.